Summary: Intermittent events where engine would not crank became more frequent and finally the starter quit working altogether. Diagnosed by eliminating likely causes (battery, battery cables, neutral switch) and then tested by applying voltage directly to starter control terminal. Finding the starter dead, it was removed and replaced.
Details: Recently we experienced several instances where the engine would not start. Turning the key to the start position resulted in just a clicking sound from under the hood but the starter would not turn. Sometimes it would work and sometimes not so once again it’s a frustrating intermittent problem.
1st thing to check when the car won’t start is the battery condition because this is the main cause of starting problems. Connected my analyzer and the battery checked out 100% perfect (voltage and capacity).
Then looked at battery terminal connections which were tight and clean. This is the 2nd most common cause of starting problems. Followed the fat red battery positive terminal wire down to the starter and it was tight and clean, as was the fat blue negative wire to the engine block.
The 3rd most likely cause of no-crank problems is a clutch switch (manual transmission) or Park-Neutral Position (PNP) switch (automatic transmission) being open. 850s do not have clutch switches from what I can tell; they were added to later model S70s, I believe. This car has an automatic transmission so it does have a PNP switch which is known to fail with age. Running the shifter up and down to freshen up the switch contacts did not help. Besides, I could hear the starter solenoid clicking which indicates that it made it past these interlocks.
A 4th possibility is a defective ignition switch but that was replaced in the past year and as mentioned the solenoid was clicking, indicating that the circuit was working.
A 5th cause of starting problems is arguably more or less likely than the others. This is the immobilizer or alarm relay which is an anti-theft feature that prevents the car from starting if the doors are not properly opened with a key or keyless remote. It was not an issue here.
Once I got it to start more frequently I noticed that there was a delay from when I turned the key to when the starter would crank. That indicates a sluggish starter solenoid, as if it was weak. Then I noticed that after releasing the ignition key from start position the starter would stay engaged for a half second or so (that whirring sound you hear when you are still cranking the starter after the engine starts running on its own). That also suggested a lazy solenoid or weak return spring or sticky solenoid plunger, all of which are starter problems.
All these diagnoses point to the starter itself so I started testing it. One nice thing Volvo did with the 850 (and likely other models) is include a handy starter diagnostic connector up near the brake master cylinder. This female blade socket makes direct connection to the starter solenoid control terminal which receives +12V when the key is turned to the start position.

Starter test port 17/1 location.
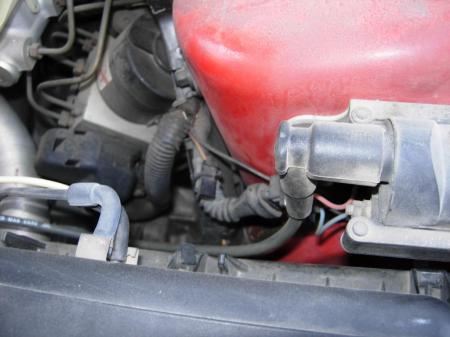
Test port near ignition coil and LH strut tower.
Actually, not quite a direct path. The test connector still goes through the PNP switch on cars with automatic transmission after this point so if you want direct connection to the starter solenoid, you’d have to connect at the solenoid. Manual transmission does go directly there. See wiring diagram for details.
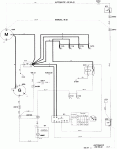
Wiring Diagram
I made up a test wire by crimping some wire to a standard 1/4″ male blade terminal. The male tab mates nicely with the test socket and gives us a handy connection to measure resistance (old starter solenoid measured high at 3.2Ω, new solenoid was 0.5Ω), voltage or apply voltage. Instead of touching the other end of the wire to the battery positive terminal, I clipped a squeeze switch in line to get better control.
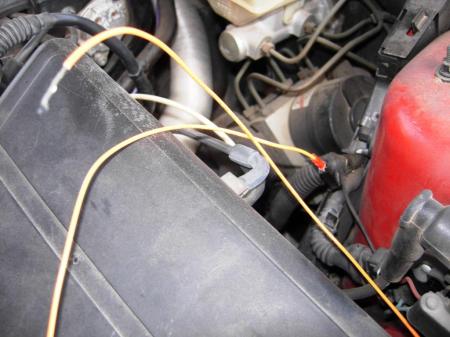
Test wire connected. Far end connected directly to battery + or through switch makes starter operate as if turning they key.
Using the switch allows me to work without an assistant to turn the key and with the first pair of quick switches the starter would crank but then the starter stopped turning and I would hear a metallic clunk when activating the switch. After several of these, I could get just a small click from the solenoid. So clearly the solenoid and/or the starter were failing quickly.
Access to the wiring terminals is made behind the snap-on cover. Be very careful with metallic tools down there; a short to anything metal will give full battery energy spark.
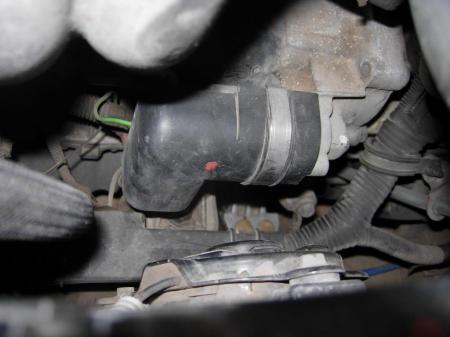
Pull this cover off to access starter terminals. No tools needed; just snaps on/off.
Unplugged the control (start) terminal and measured voltage with respect to the engine block. When energizing the test port I measured +12.5V so I know the starter is getting proper control voltage. That clears up any doubt that the solenoid or motor were bad.
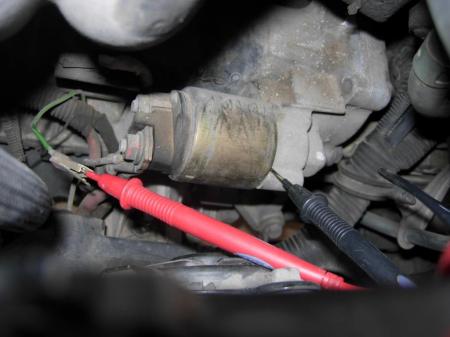
Measured control voltage at the disconnected wiring terminal. +12V here with no start means a bad starter or solenoid.
Tried tapping on the solenoid and starter to see if this would make it work again. Don’t laugh, this often gets a failed starter to work one or two more times if something is stuck or if the motor is in a dead spot. No good and so now the intermittent problem has become a permanent problem. Clearly the solenoid or starter motor has issues and the whole thing needs to be replaced.
Replacing the starter is not difficult but you do have to remove several things to gain access.
First you disconnect the battery negative (-) terminal after verifying you have the radio code. Then you remove the control module cooling pipe, air duct to air cleaner, fan shroud assembly and relays and vacuum valves mounted to it, which requires disconnecting various cables and hoses. Finally remove throttle pulley cover and solenoid cover if not already done.
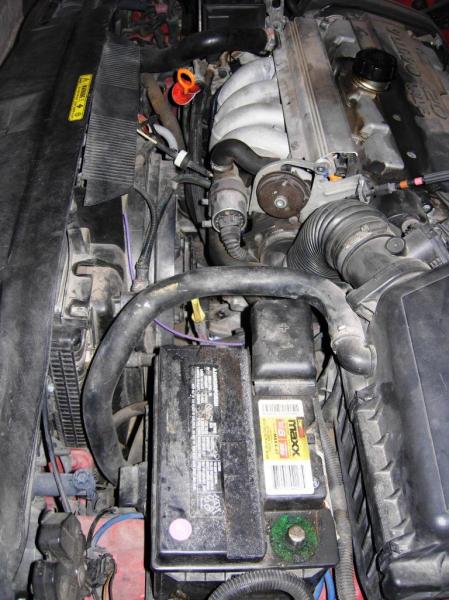
Various air ducts and throttle cover removed for access.
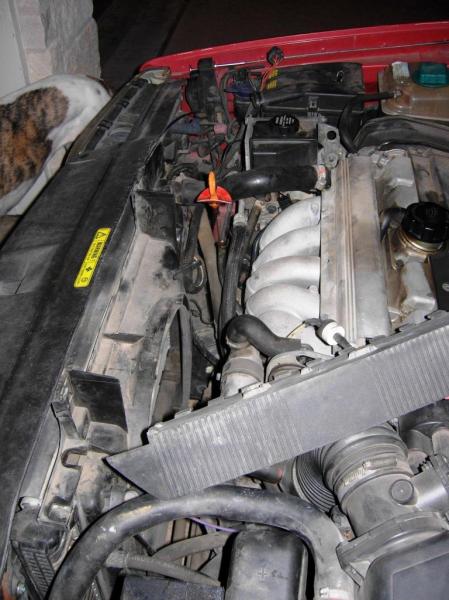
Fan assembly and associated wires and hoses removed for access to starter.
Now we can remove the starter itself. Start by unbolting or unplugging all wires from the starter.

Cables disconnected from starter solenoid.
Then remove three bolts holding the starter to the engine block and lift the starter out. Shop manual and other procedures do not mention unfastening this harness clamp…
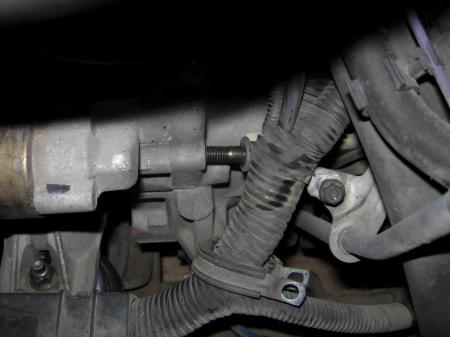
Harness clamp must be removed to get wrench on lower bolt.
…or removing the throttle body intake pipe, but both had to be done for access.
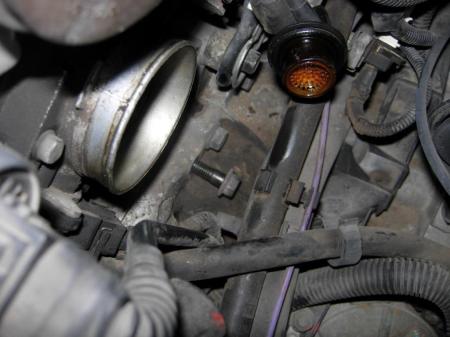
Upper bolt can’t be reached without removing the throttle body inlet pipe.
Once these three bolts are removed, the starter should just lift out. If it’s really frozen in place it might take some careful prying but this one came free easily.
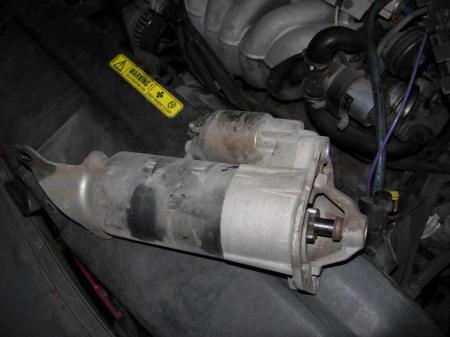
Starter should simply lift up and out once the three bolts are removed.
The mounting bracket on the left is separate from the starter so needs to be unbolted from the starter for use with the new part.
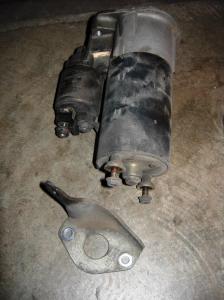
Bracket needs to be unbolted from the old starter…
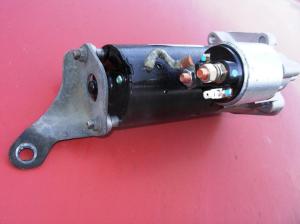
…and transferred to the new starter.
Note the photos shown are for a 1997 model 850. Older 850s may have a slightly different starter as noted in the factory manual.
Note also this locator pin which hopefully stays with the starter. If it sticks to the engine you will want to pull it out; new starter should come with a pin.
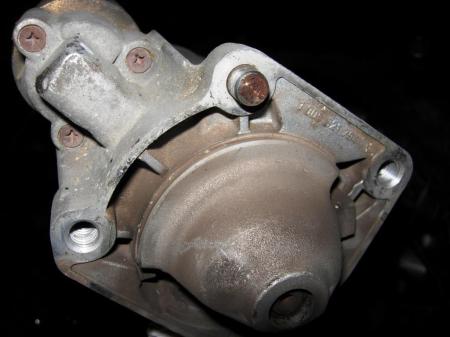
Locator pin engages with hole in engine housing.
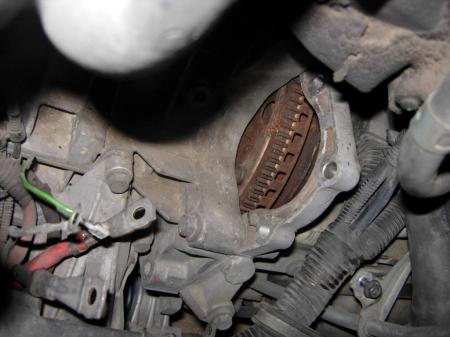
Rare peek at engine flywheel which engages with starter pinion gear to crank engine.
Tried to unscrew the solenoid from the starter to inspect the guts but could remove only one of three screws, even using an impact driver after spraying penetrating oil, so gave up on doing an autopsy. Wish I knew what was going on inside there.
While many people insist on factory parts only, like several other tasks on this project I choose to save money by using a high-quality re-manufactured starter.
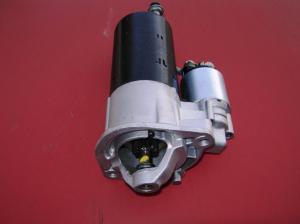
Shiny new starter.

I’m saving hundreds of dollars and I doubt that the quality difference will be noticeable in the short term. Maybe 15 years out but I don’t think this car will still be around that long. Besides, my experience with reman parts is that they often are factory parts that have been cleaned, renewed and tested so are as good as new. This one had the Bosch ID stamps on it so is likely mostly factory parts.
As for the solenoid, I believe that there are two coils: one higher current (lower resistance) to pull the plunger in and one lower current (higher resistance) to hold the plunger in after disconnecting the high-current coil. Since the old bad coil measured 3.2Ω and the new one measured 0.5Ω, I’m guessing that the high current coil was open or the disconnect switch was stuck open. Either way, it would leave only the holding coil in the circuit which is not strong enough to pull the solenoid closed, at least reliably.
New starter is installed in reverse of the removal procedure.
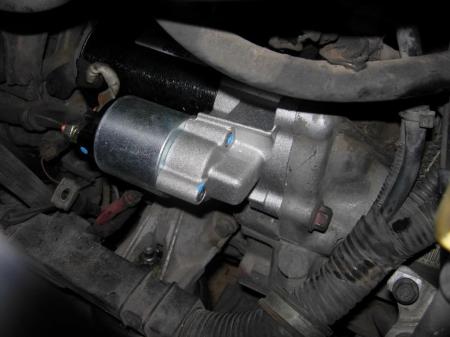
New starter bolted in place…
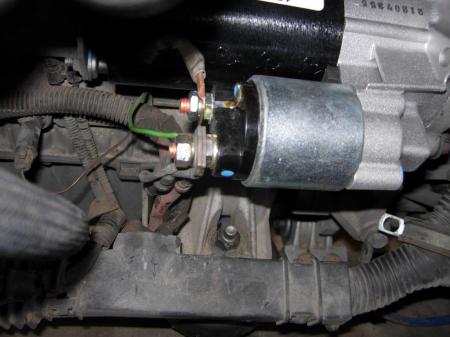
…and wires attached.
Put all the ducts, fan, hoses, relays and covers back in place and ready to check after reconnecting the battery negative terminal. Key in and it starts right up. No surprise.
$140 for an remanufactured starter.
Technical Notes
The main parts of a starter are the motor and the solenoid which are combined in one assembly. The motor is just a high-torque, high-current DC motor that is strong enough to spin the engine.
The solenoid does two important jobs and is often the culprit with a bad starter. First it switches the battery connection to the motor winding, like a big high-current relay or contactor. Second it pushes the pinion gear out to engage the engine flywheel teeth so that the spinning motor is coupled to the engine for starting and releases it once the engine is running. These two things are accomplished in one linear motion by an electromagnetic field from the solenoid coil.